Precision Matters: Enhancing Drilling Accuracy through Effective Practices
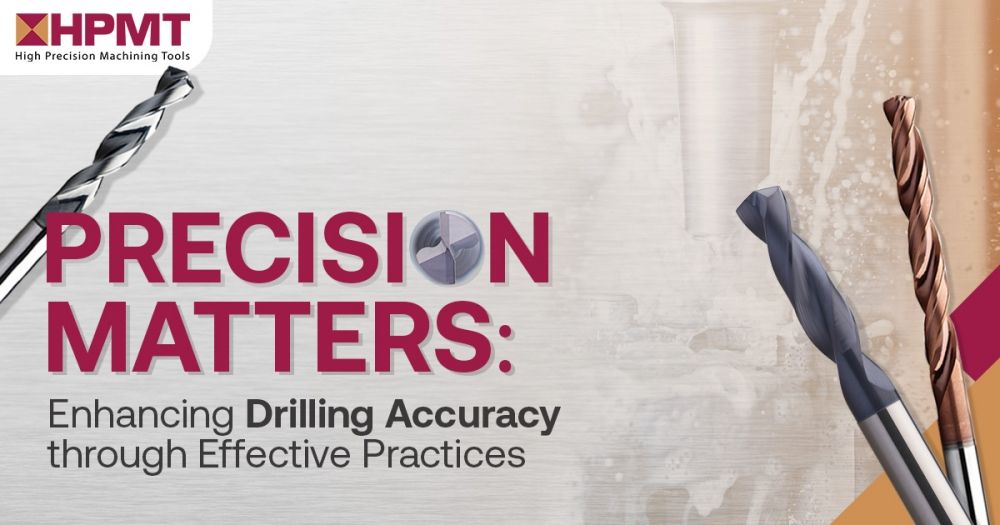
Drilling is one of the most complex machining processes. It involves creating accurate holes in materials using drills or other drilling methods. To achieve optimal results, it is essential to follow best practices that ensure improved accuracy. This article will explore the fundamental concepts of precision drilling and provide valuable insights into ways to enhance drilling accuracy.
By selecting the right drill with appropriate geometry, you can enhance accuracy and achieve superior results in your drilling operations.
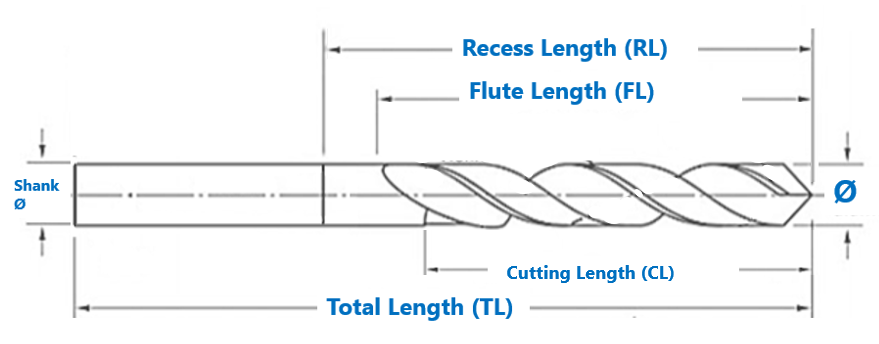
Four Common Drilling Methods:
Drilling Operation Process:
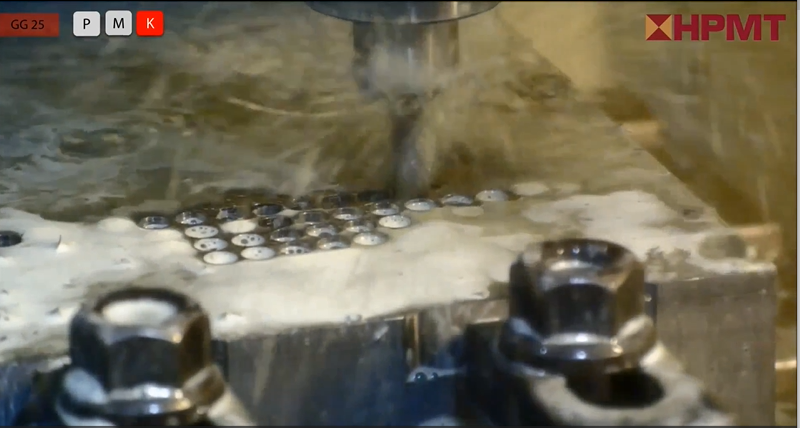
It is crucial to follow a systematic operation process to ensure accuracy and efficiency during the drilling process. The following steps outline the key stages of precision drilling:
Tool Selection: Choose the appropriate drill bit or drilling method based on the material, hole size, and desired accuracy. HPMT provides a diverse range of drills, ensuring you find the perfect tool for your specific requirements.
Cutting Parameters: The cutting parameters, such as spindle speed and feed rate, are set based on the material being drilled and the drill bit's specifications. These parameters ensure efficient material removal and prevent tool wear or breakage.
Coolant Application: Depending on the material being drilled, coolant or lubrication may be applied to reduce heat and friction, prolong tool life, and improve hole quality. HPMT Industries offers coolant-through drills that ensure efficient chip evacuation and cooling.
Hole Inspection: After drilling, the resulting hole should be inspected for accuracy, size, and surface finish. If one of the breaks we can replace it with the other tools and any necessary adjustments or rework may be performed. Monitor the process closely, ensuring the drill remains aligned and perpendicular to the workpiece always.
To achieve enhanced drilling accuracy, consider the following tips and techniques:
Inspection and Measurement: Regularly inspect and maintain your drilling tools to ensure they are in optimal condition. Replace worn-out drill bits and check for any signs of damage that may affect accuracy. Additionally, regularly inspect and measure the drilled holes to meet the desired specifications. This allows for any necessary adjustments or corrections to be made promptly.
Workpiece Stability: Securely fix the workpiece to prevent movement or vibrations during drilling. This helps maintain precise hole placement and prevents deviations caused by workpiece shifts. Use a stable and rigid drilling setup to minimize any deflection or movement of the drilling machine or workpiece. This can be achieved using a sturdy drilling machine, rigid work-holding devices, and appropriate support structures.
Operator Skill and Training: Provide proper training to operators to handle cutting tools effectively and understand drilling techniques. Skilled operators can optimize drilling parameters, monitor the process closely, and adjust as needed for improved accuracy. Our drilling handbook is a comprehensive guide, equipping operators with the necessary knowledge and skills to ensure precise and efficient drilling operations.
In the world of precision drilling, accuracy is paramount. You can achieve exceptional results by following best practices and using high-quality drills, such as those provided by HPMT Industries, Consider the appropriate drilling method, and adhere to a systematic drilling operation process. Additionally, incorporate maintenance routines and invest in stability-enhancing measures to further enhance accuracy. With these measures in place, you can take the first step towards achieving precision drilling and unlocking new levels of accuracy in your operations.